----- スポンサーリンク -----
目次
Index
はじめに
安価で精度の高い3Dプリンターを個人でも入手できる時代となりました。
自分でデザインした3Dデータを自らが造形し、初めて手に取った際の喜びや感動は、何者にも置き換えることはできません。
そんな3Dプリンターですが、自らが自由に積層方向を決めて造形できる楽しさがある一方で、個人やエンジニアが初めて造形を行う際、ぜひ注意しておいていただきたい「積層方向」に関するポイントがあります。
私はメカエンジニアであるにも関わらず、初回の造形品で一発目の組み立てを行った際、いきなり折れてしまうといった、失敗をしてしまいました。
その失敗経験を元に、今回は「3Dプリンターの積層方向に対する強度や造形時間の関係」について、少し触れていきたいと思います。
----- スポンサーリンク -----
プリント工程
まずは詳細に入る前に、3Dプリンターのプリント工程について軽く触れておきたいと思います。
3Dプリンターのプリント工程は、1層1層と断面(2D)を積み重ねていくことで、形状(3D)を作り上げていきます。
3Dプリンターの造形方式には、光造形をはじめ、様々な方式がありますが、基本的にどの方式も同じプリント工程で造形が行われています。

プリント工程
1. 水平方向にノズルを走らせて1層目を造形
2. テーブルが1段下がる(下がり量:0.1mmレベル)
3. 水平方向にノズルを走らせて2層目を造形
4. テーブルが1段下がる(下がり量:0.1mmレベル)
5. (以降同様に完成まで繰り返し)
この積み重ねですが、積層していく方向により、強度と造形時間に大きな影響を与えます。
よって、安易に積層方向を決めるのではなく、造形品の使用目的に応じた積層方向を決めていく必要があります。
積層方向と強度の関係
完成した造形品の表面を拡大すると、下図のような状態になっています。
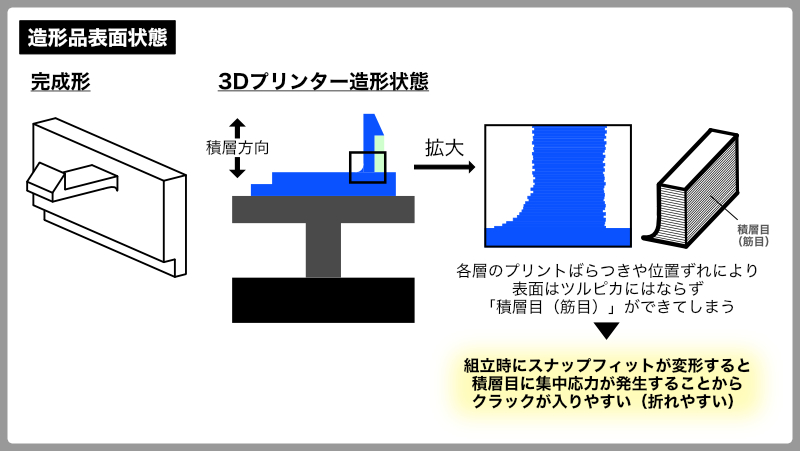
現実的には加工ばらつきが発生することから、表面は面一にはなっておらず、凹凸ができています。
この凹凸は筋目になっており(レコード板の表面をイメージ)、造形品に力が加わる方向によっては、集中応力が発生することから、筋目に沿う形で直線状の亀裂が入りやすく、最悪は破断(折れる)に至ります。
このようなことから、樹脂製のスナップフィットを用いた部品など、たわませながら組み立てるような部品は、たわみ方向を想定し、集中応力が発生しにくい積層方向で造形していくことが重要なポイントとなります。
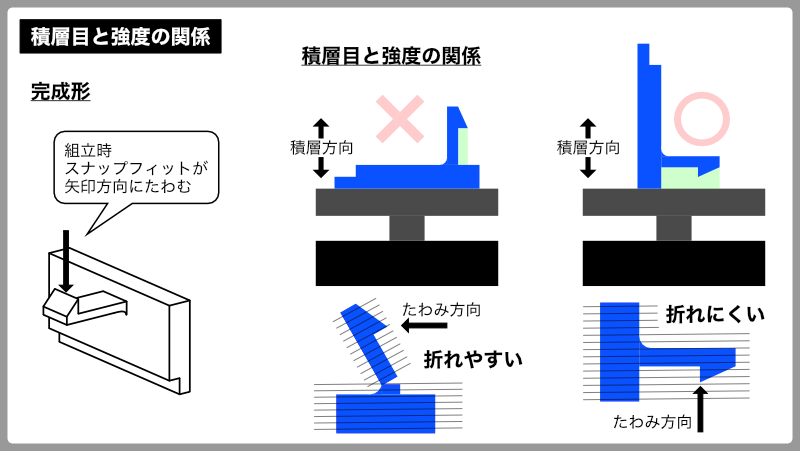
新規形状の機能確認や、組み立て確認を目的とした試作である場合、この積層方向と強度の関係は十分に注意をして造形を行ってください。
私のように造形したものの、一発目の組み立てで壊れてしまい、上司に悲しい報告をしなくてすむようにしてください。(笑
----- スポンサーリンク -----
積層方向と造形時間の関係
前項の「プリント工程」で説明したように、3Dプリンターの特性上、造形方向と造形スピードとの間には、以下のような関係があります。
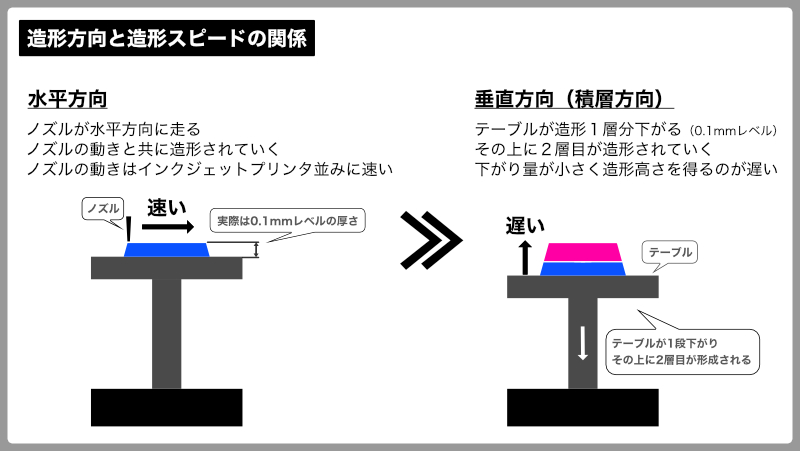
造形方向 | 造形スピード |
---|---|
水平方向 | 速い |
垂直方向 (積層方向) | 遅い (0.1mmレベルの薄さで1層1層積層していくため完成品の高さになるまで時間がかかる) |
よって、造形時間の最短を目指す場合、テーブルに対し造形品が低背となるような積層方向がベストとなります。
特に企業で働いているエンジニアは、退社時に3Dプリンターを仕掛けてから翌朝出社後に完成した造形品を取り出すといった、造形時間をあまり気にしない使い方が一般的かと思いますが、造形時間の短縮はプリンターの消費電力の削減に繋がり、コスト削減へと繋がります。
最終的には地球環境の貢献にも繋がりますので、造形時間が最短となる積層方向を見出すことが重要となります。
強度と造形時間を両立させた積層方向
強度と造形時間を考慮した積層方向は、造形品の形状が単純であればあるほど、さほど悩む必要はありません。
ただし、実際に製品開発が行われている現場で生み出された部品は、とても複雑な形状をしています。
特に樹脂部品においては、板金部品と異なり、1部品に多くの機能を持たせることから、より複雑な形状となっています。
例えば下図のような樹脂製のボックス部品の場合、どのような積層方向がベストでしょうか?
造形の目的は、組立性の確認が主ということで考えてみたいと思います。
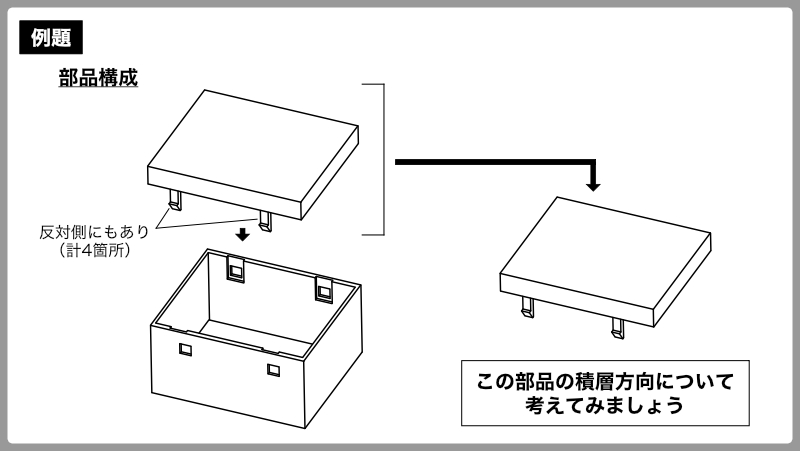
まずは強度と積層方向について考えてみたいと思います。
4箇所にスナップフィットが設けられており、組立時にこの部分がたわみます。
よって、スナップフィットが折れにくい方向へ積層していく必要があり、「高背置きの案」が強度面からみてベストの案となる一方、テーブル面からの造形品高さが最大となり、造形時間が最長となる欠点を伴います。
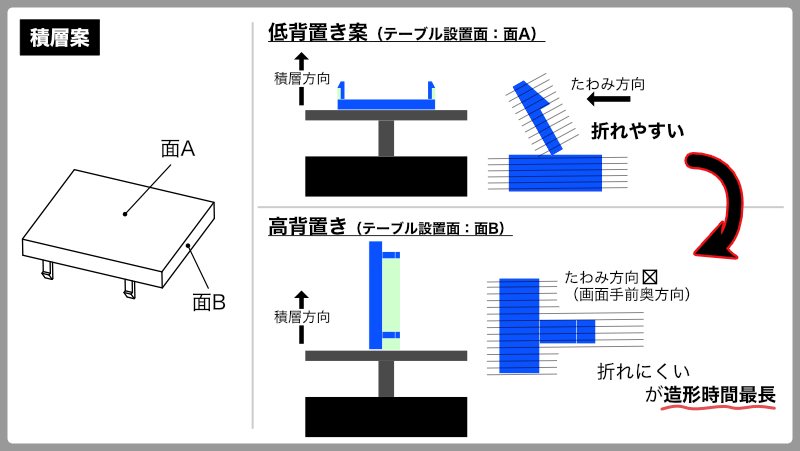
ここで将棋に例えると「詰み」の状態となり、高背置きの案で造形を進めるかと思いますが、もう1歩踏み込んだ打開策について考えていきたいと思います。
その打開策ですが、一般的には造形品の主だった一面をテーブルに設置する形で積層していく案を考えがちですが、少し型破りな方法として、造形品がテーブルに対して斜め置きとなる方向に積層していくことで、強度と造形時間の双方を両立させていくことが可能となります。
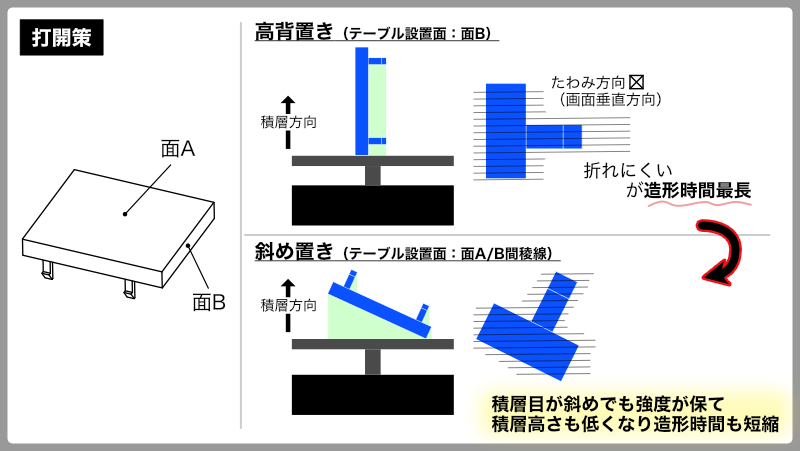
斜め置きは、実際の試作でよく使う技の1つなので、引き出しの1つとして覚えておくと、いずれ何かの役に立つかと思います。
----- スポンサーリンク -----
最後に
現段階において3Dプリンターの造形は、試作目的で使われることが一般的です。
ただし、プリンターの造形スピードが上がり、造形品の材質自体もより進化していくことで、実際の製品部品への展開が期待されています。
3Dプリンターでの量産が可能になると、樹脂部品においては金型の抜きを考慮する必要がなくなり、抜き勾配が不要で、金型を抜くためのユーザーにとっては意味不明となる角穴も設ける必要がなくなります。
また、金属製のダイキャスト部品においては、樹脂部品と同様の効果はもちろんのこと、自動車のシャーシなどをはじめ、これまで加工上の都合で複数の部品に分割していたものを一体化させることで、より高い剛性や強度が得られるようになり、組立ラインにおいても、組立工数の削減を狙っていくことも可能となります。
エンジニアにとって、上記のような加工上の制約がなくなることは、より自由度の高い設計が可能となります。
一方、自由度が高まることで、型に縛られない「より多くの発想力」と、多くの発想から最適解へと導く「本質を見抜く力」がポイントとなってきます。
メカエンジニアと言えば、CADや工具をかっこよく使いこなしている姿を想像しがちですが、様々な発想や情報の中から本質をだけを見抜き、行動へ移していく実行力が、より求められる時代になってきたように思えます。
これからの時代。
モノだけを形にするだけではなく、完成に至るプロセスについて、より重要視して取り組むエンジニアこそが、これからの時代をリードしていくための、鍵になっているのかもしれませんね。
色々とやることだらけで大変な毎日ですが、1つずつ着実にこなしていきたい、今日このごろです…