目次
Index
はじめに
車載部品や電化製品を思い浮かべると、樹脂筐体の内部には基板など様々な部品が収納されています。
これらは組立を行うために、少なくとも筐体を2分割(2部品)で構成しておく必要があります。
この2分割にした個々の筐体部品を、ねじや接着剤などを用いて固定することにより、1つの筐体として機能させることができます。
ここで固定方法について着目してみると、ねじ固定の場合は当然のことながら、ねじ自体のコストや、ねじ締めといった組立工数が発生します。
また、接着剤による固定の場合は、接着剤自体のコストは当然のこと、組立の観点でみても安定した均一な塗布方法の確立や硬化時間の確保、接着後分解できないといったマイナス面を持ち合わせています。
これらの課題を解決する手段として、樹脂筐体ではスナップフィット(嵌合爪)を用いた固定方法がとられています。
筐体部品にスナップフィットの形状を付加することで、ねじや接着剤といった別部品が不要となり、ワンタッチで組み立てることができ、分解も可能となります。
このスナップフィットを用いた筐体設計ですが、コストアップや量産性を低下させないよう、過剰で複雑な設計を避け、必要最小限の機能だけで構成した設計が必要となります。
エンジニアに応じで様々な設計思想があるかと思いますが、今回は単純な箱形状をした樹脂筐体を例に、スナップフィットを用いた筐体設計の進め方について、考えていきたいと思います。
スナップフィット(嵌合爪)を用いた筐体設計の進め方
まずは、スナップフィット(嵌合爪)を用いた筐体設計を進めていくにあたり、下図のような題材を例にして、考えていきたいと思います。
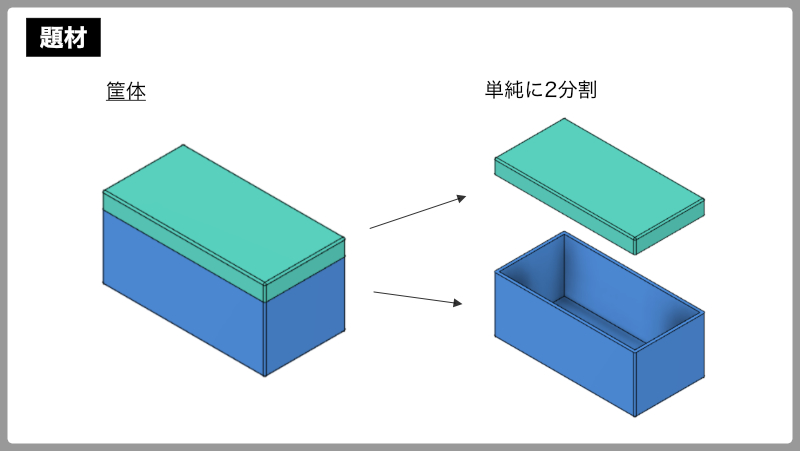
この単純に2分割にしただけの箱を、スナップフィットを用いた筐体に仕上げていきたいと思います。
大きな設計手順は以下の流れとなります。
手順
1. スナップフィットをどの部品に設置するかを考える
2. スナップフィットをどの側面に設置するかを考える
3. 嵌合相手となる部品にスナップフィットに対する角穴を反映する
4. スナップフィットの外れ防止用のかみ合わせを設ける
5. 筐体の外側から内側方向に対する変形防止用のかみ合わせを設ける
6. 筐体の内側から外側方向に対する変形防止用のかみ合わせを設ける
ここでいきなり結論ですが、上記手順に沿って私なりに考えた筐体形状は下図となります。
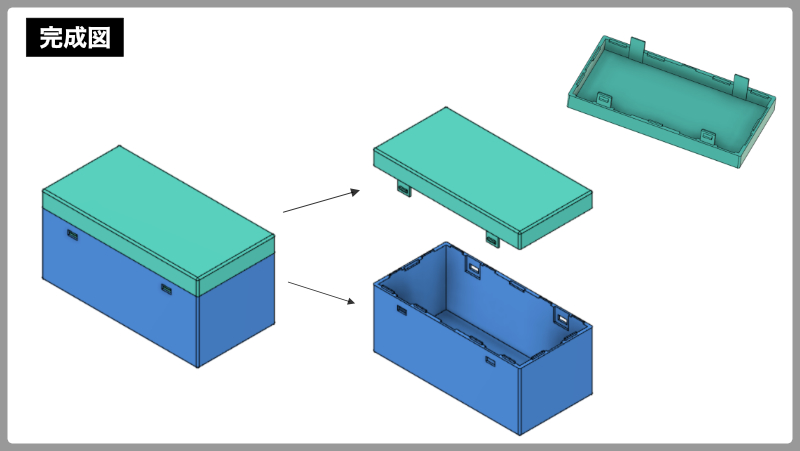
それでは各手順ごとに、完成図に行き着くまでの過程を見ていきましょう。
手順1. スナップフィットをどの部品に設置するかを考える
スナップフィットは、下図の方向に変形すると外れます。
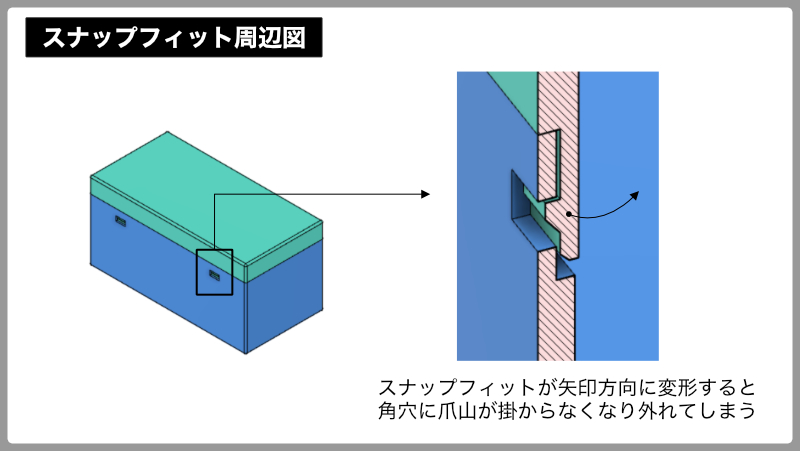
よって変形しにくい部品にスナップフィットを設置することで、より高い嵌合力を得ることができます。
それでは、今回の題材を見てみましょう。(「蓋」と「本体」という部品名を付けました。)
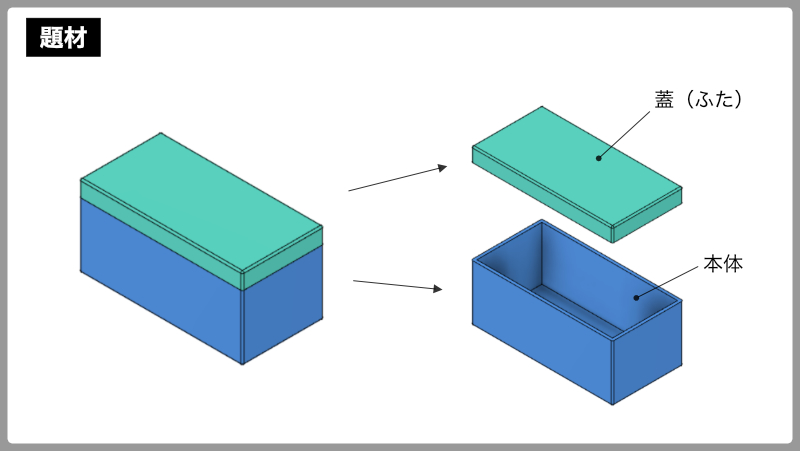
この2部品のいずれかの側面に、スナップフィットを設置する必要があります。
この2部品を比較した場合、どちらの部品の方が変形しにくいでしょうか?
単純な片持ち梁ではありませんが、腕の長さが短い蓋のほうが変形しにくいといった見方ができます。
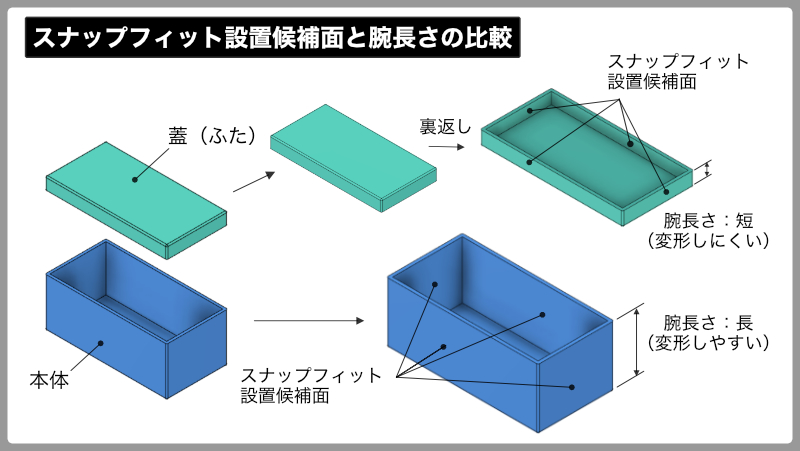
よって、スナップフィットは下図のように、より変形のしにくい「蓋」の方に設置することにしました。
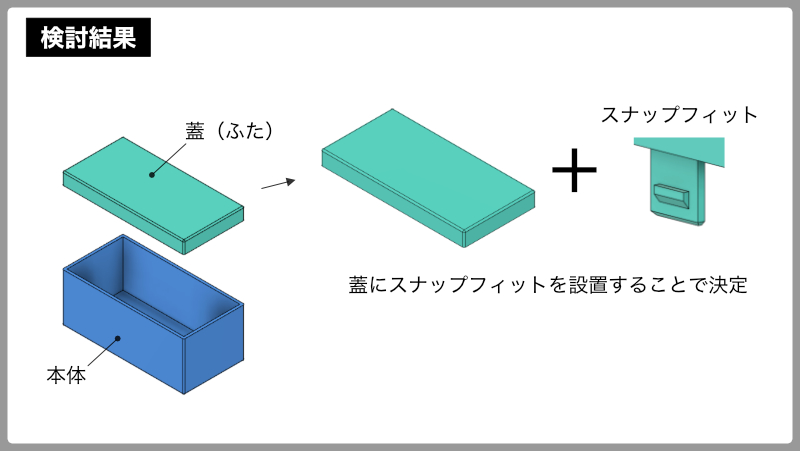
手順2. スナップフィットをどの側面に設置するかを考える
それでは、蓋に対してどの側面にスナップフィットを設置するのがよいか、考えていきたいと思います。
設置候補となる面は、下図左側記載の2つの案が考えられます。
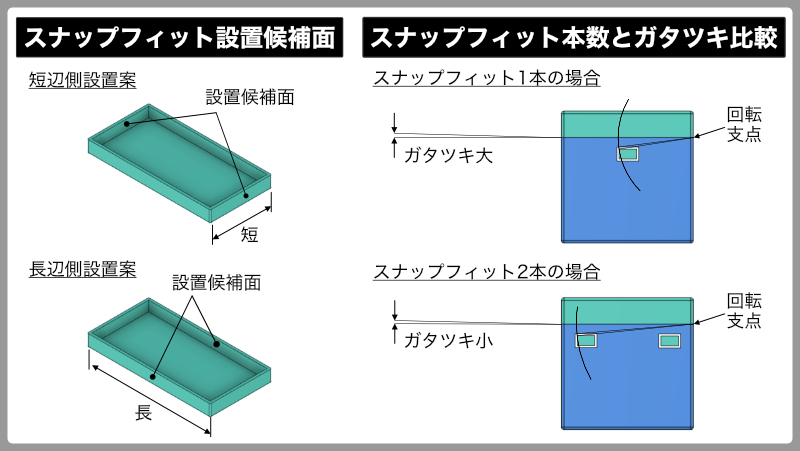
単純に設置面の長さだけを比較すると、短辺側設置案の方が、腕の長さが短く変形しにくいため、スナップフィットの設置面として好ましいといった見方ができます。
次に、スナップフィットの設置本数ですが、1本より2本の方が、嵌合強度をより高めることができ、回転支点からスナップフィットまでの距離が長く取れることから、部品間の回転角=ガタツキを小さくすることができるため、各側面ごとに2本以上の設置が好ましといった見方ができます。
よって、短辺側設置案で示した候補面に、スナップフィトを2本ずつ計4本設置で進めていきたいところでありますが、ここでもう1つ必ず考えておかなければならないことがあります。
それは、蓋や本体といった部品単体だけではなく、組立状態における変形挙動の想定です。
具体的には、組立状態において蓋や本体に力がかかった場合、スナップフィットをはじめとする筐体全体が、どのような変形を起こすのかをイメージしておく必要があります。
組立後の蓋や本体にかかる力に対し、考えられるスナップフィットの変形挙動は下図4パターンが想定されます。
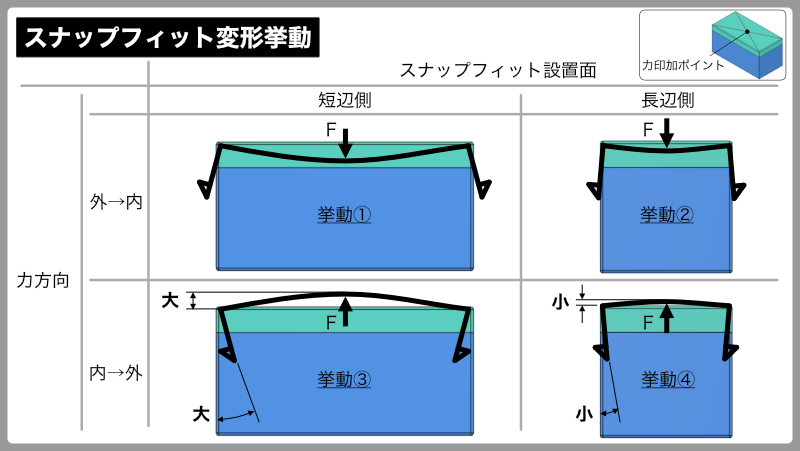
これらの変形挙動を見てみると、挙動① と 挙動② については、スナップフィトの爪山が本体側へ食い込んでいく方向であることから、より外れにくくなるため、問題ないといった見方ができます。
一方、最も問題となるのが 挙動③ となります。
蓋の中央付近に内側から外側方向へ力が加わった場合、スナップフィットが外れてしまう方向の挙動を示し、問題ありといった見方ができます。
挙動④ についても同様のことが言えますが、両端支持梁として考えた場合、挙動③と比較して、腕の長さが短いことから、変形しにくい(外れにくい)といった見方ができます。
これらの変形挙動から、冒頭では短辺側設置案で示した候補面に、スナップフィットを設置しようと考えていましたが、組立後に想定される蓋=スナップフィットの変形挙動から、よりスナップフィットが外れにくい、挙動④=長編側設置案を採用することにしました。
よってスナップフィットを設置した状態は下図のとおりになりました。
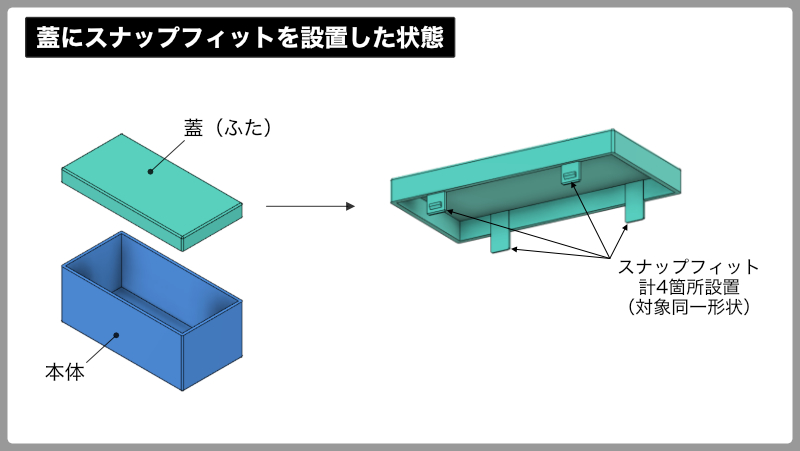
嵌合後のガタツキを小さくしたいのと、スナップフィットが変形しにくいよう、極力端の方に設置しました。
あまり端に寄せすぎると、本体側も変形しにくく組立が固くなることから、少し端から距離をとっています。
手順3. 嵌合相手となる部品にスナップフィットに対する角穴を反映する
蓋に設置したスナップフィットの形状に合わせ、本体側に角穴を反映していきます。
単純にスナップフィットの爪山に合わせる形で角穴だけを反映してもよいのですが、組立時に蓋を本体へ乗せる際の、ある程度の目安(位置決め)を設けておきたかったため、本体側に凹形状を設けることにしました。(爪山が凹形状に嵌ることで、ある程度の位置決めができる)
また、蓋に設置するスナップフィットの形状は、爪山周囲に平面を設けました。
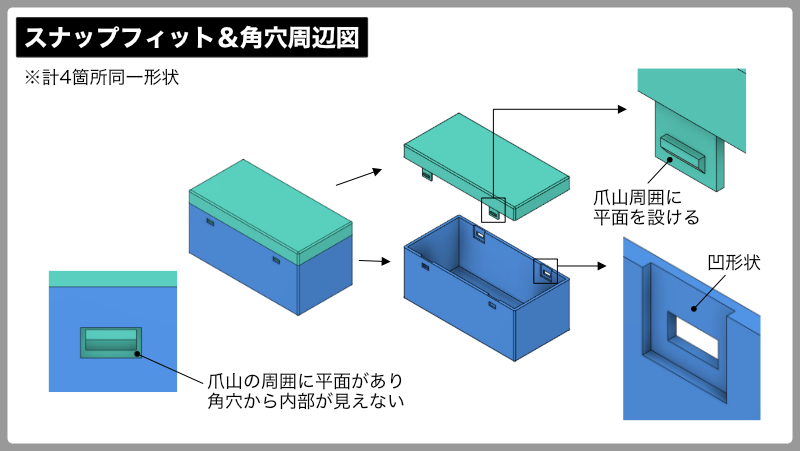
この平面により、筐体の外側から角穴を通して内部を見えないようにしています。
筐体外部からの異物も入りにくくなり、電子機器で角穴周辺に基板があるような場合には、角穴周辺を手で触れた際に発生する静電気に対し、基板までの絶縁距離を稼ぎ出す効果もあります。
嵌合状態(嵌合断面)については、手順1の冒頭にあるスナップフィット周辺図を参照してください。
手順4. スナップフィットの外れ防止用のかみ合わせを設ける
手順3までで主要となるスナップフィットの設置が完了しました。
蓋と本体とがスナップフィットで嵌合できるようになり、基本的に1つの筐体として機能するようになりました。
ここからの手順は、組立後の筐体、すなわち製品状態に対し、より改善を加えパワーアップさせていく作業になります。
今回の手順4は、嵌合状態にあるスナップフィットをより外れにくくするための改善を加えていきます。
スナップフィットは構造上、スナップフィットの爪山と相手側の角穴が離れなければ、外れることはありません。
言い換えれば、スナップフィット周辺に外力がかかった際、お互いが追従する形で変形すれば、外れることはないのです。
これを実現させる方法として、蓋と本体との間に、かみ合わせを設けておきたいと思います。
具体的には、スナップフィットの周辺に下図のように凸凹からなる、かみ合わせを設けます。
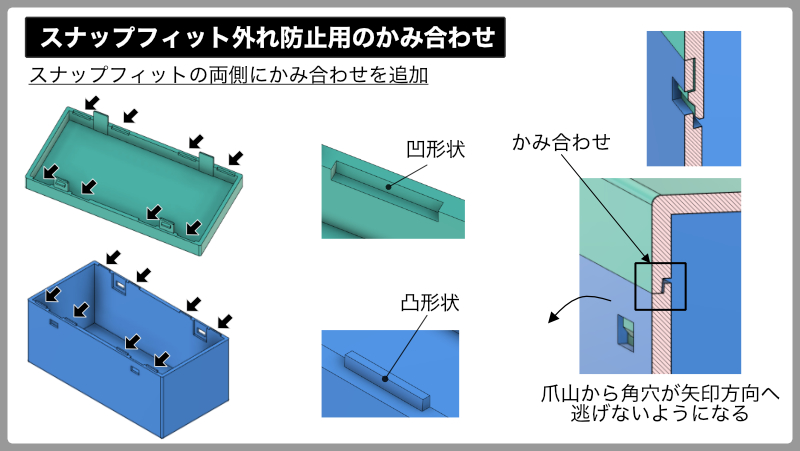
このかみ合わせを設けることで、筐体外部からスナップフィットの根本に位置する蓋の側面を押し込んでも、かみ合わせを通じて角穴がスナップフィットに追従し、お互いが離れることはなく、嵌合状態を保つことができます。
また、筐体内部からピンポイントに角穴周辺に力がかかっても、同様にかみ合わせを通じてスナップフィットが角穴に追従し、嵌合状態を保つことができます。
ちょっとした形状ですが、よりスナップフィットが外れにくい改善を加えることができます。
ここで1点注意しておきたいことがあります。
それは、スナップフィットとかみ合わせの間隔です。
この間隔が遠すぎると、追従効果が小さくなります。
一方、近すぎると、追従効果は高まりますが、組立時にスナップフィットを嵌合させる際、かみ合わせがうまくかみ合わず、凸形状が筐体の外側に飛び出してしまうことがあります。
このあたりの距離感は、既に上市されている実績のある量産品を参考にしたり、3Dプリンターによる試作で組立検証を行うことで、精度を上げることができます。
手順5. 筐体の外側から内側方向に対する変形防止用のかみ合わせを設ける
手順4までで、スナップフィットに関する最後の味付けが完了しました。
ここからは筐体全体の強度を上げるべく、最終仕上げへと移っていきます。
筐体全体を見渡すと、蓋と本体との合わせ面が接着されていないことから、合わせ面の周辺が最も変形しやすくなっています。(指で押し込むとペコペコするイメージ)
ここで筐体側面の内側方向に対する変形を想像したいと思います。
下図左側記載の、なにも支持のないポイントが、筐体の内側へ最も大きく変形する箇所となっています。
特に蓋と本体を比較すると、本体側の方が深さがあり、力学的に言うと腕が長いことから、大きく変形します。
この変形に対し、ここでも新たにかみ合わせを設けることで、対策を行っていきます。
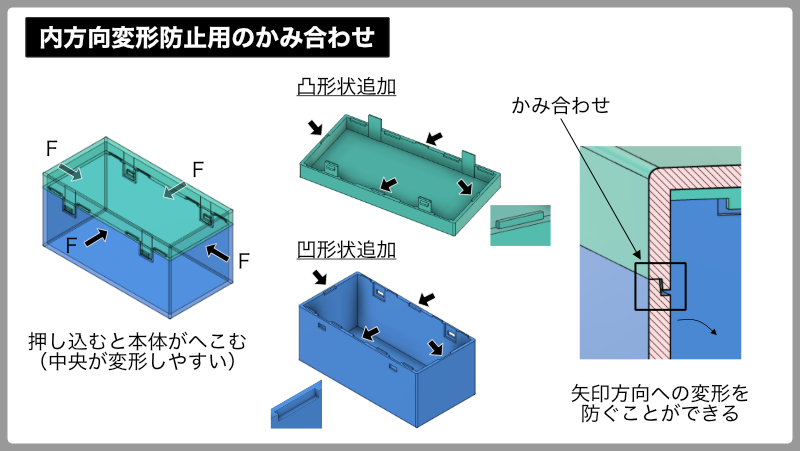
以上で筐体内側方向に対する変形を防止することができました。
手順6. 筐体内側から外側方向に対する変形防止用のかみ合わせを設ける
最後に、手順5と反対方向の力、すなわち筐体の内側から外側方向に対する変形対策を行っていきます。
長辺側はスナップフィット周辺にかみ合わせが設けられていることから、既に変形防止が行われているといった見方ができます。よって長辺側はなにもせず、現状キープで進めたいと思います。
残りの短辺側を見てみると、力に対して支持するものがないため、かみ合わせを新設し、対策を行います。
下図のように、既設のかみ合わせが中央にあるため、これを避ける形で両脇に設置する形となります。
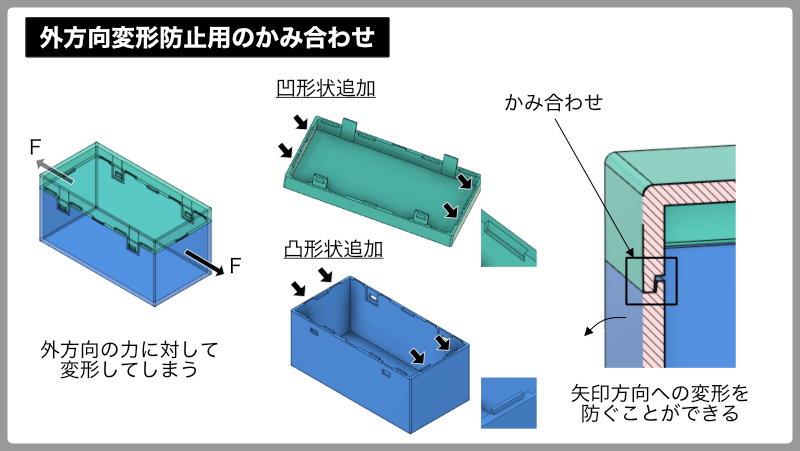
以上で、スナップフィットを使った筐体が完成となります。
最後に
スナップフィットを使った筐体設計は、手順1と2が大きなポイントとなっています。
この2つの手順で嵌合強度を確保するべく骨格が生み出されています。
家の建築で言うところの、大黒柱といった位置づけとなりますので、筐体設計の中でも、より多くの時間を取り、最適な設置案を考え出すことが、設計の後戻りを防ぐ意味においても、とても大切に思えます。
想定される外力や求められる嵌合力に対し、様々な設計アプローチがあるかと思います。
また、エンジニアによっても、様々な設計思想を持たれているかと思います。
今回は単純に蓋と本体のみで考えていきましたが、筐体内部には他の部品もあるでしょうし、筐体を設計していく上で制約事項が生まれてきます。
様々な制約事項をクリアすべく臨機応変な対応をしていく中で、今回の例がなにかの参考や、意見交換などのきっかけになれば、私自身とてもうれしく思います。